ABOUT THE COMPANY
Metal-on Industries lines
1) Leakage sealing in live pipe lines during flow without interrupting the production processes.
2) Metallizing through hot or cold spraying, by using an "arc spray" or "flame spray" as a mean of
3) Dynamic balancing for rotating equipment with a portable equipment .
4) Repair and reconstruction of industrial machinery.
5) Production of handling systems, worm conveyers, elevators and turning-over facilities.
6) "Trevi test" - an examination and calibration of safety valves in live lines during the systems operation
The manager/ plant's engineer
  the METAL-ON company is the outcome of a small-scaled businedd
which had started engaging in the filds of industrial maintenance in 1985
and consisted of 3 people : myself and two other workersand a tiny
amount of equipment.
  yet our persistenece and the faith large and serious clients had had in
us, alike the Israel Oil Refineries, enabled ud to prove that we are capable
of overcoming market's demands in our fields. As time went by we
have set ourselves a goal which is to aspire to be angaged in maximum
lines of industrial maintenence.
  today, our company amploys angineers, pratical engineers,
economists and skillful professionals. today, our company consists of 23
people.
  An additional goal we have set to ourslves was to reach the highest
degree of quality abd for this prupose we srarted working according to a
system of quality standards.
  Nowadays, the company has almost on competitors in the field of
leakage sealing, and a handful in the field of metallizing.
  The compamy has business relations with worldwide cpmpanyies : in
germany, france, switzerland, and canada
  We will be honred to add you to our distinguished list of
customers. Futher on you will find additional information abut the
company and it's lines of business.
Yours faithfully,
Ami cohen
Managing - director
Back to top ...
Leakage sealing in live piping
Did you know?
Thousands of dollars are wasted in the industry every month brcause of
steam, gas, fluids leakage from the production system. The fear of the
losses involved in disconnecting piping lines in the production system
delay the repair of the leaks, and results in the development of dozens of
points of leakage in the system.
The trouble is that theses points of leakage are very costly. Acareful
cakculation shows that a keakage thrugh a nozzle developing to the size of
1/8" in a pressure of 300 PSI, reslts in a loss of 141,000 pounds of steam
a month at a cost of approximately 500$.
Metal-On has the efficient solution toprevent this unnecessary waste
This olution is implemented by the method of leakage sealing in live
pipes, meaning, leakage sealing during the operation of the leaking
production system
BEFORE
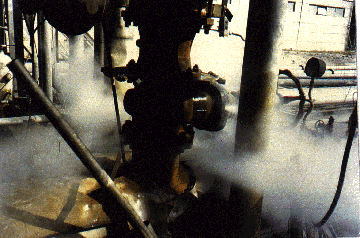
AFTER
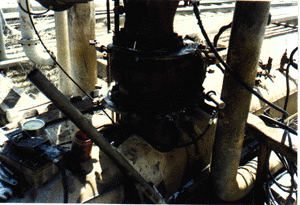
Back to top ...
Leakage sealing in live lines - the method
Leakage sealing in live lines is a unique system developed in order to
perform leakage repairs in piping as the material continues to flow and
with no disruption to the production processes.
This method enables us to seal leakage between flanges, glands and
valves, in faulty welding areas, in bolted fittins, heat exchangers, turbines
and so on without disconnection or dismantling the fitting.
Metal-On which has penetrated to field of sealing and has speialized
in a wide veriety of the related activities, is a leading company in this field
in israel
Back to top ...
implention
Leakage sealing in live pipes is performed by Metal-On by using various
techniques, while using special auxiliary accessories, according to the type of
facility or the leaky location.
First, the leaky area is isolated through a special technique and or an auxiliary
fitting, and then a special sealant is injected to the fitting. (The material does not penetrate the system).
This process provides an absolute and reliable sealing
Back to top ...
The independence of the sealing in the flowing material
Metal-On has the ability to seal leakage of most kinds of fluids and gases prevailing in the
general and chemical industry. These materials can be sealed in temperatures of up to 700°C and at all pressures.
These material include various types of -
·   water
·   oils
·  fuels
·  acids
·  compressed air
·  steam
·  noble gases
·  explosive gases
Back to top ...
And in the future
The means of sealing live pipes described above, enable to continue the
operation of the sealed facility (and of the whole production system)
under the original maintenance conditions.
The sealing performed by Metal-On's specialists is a non-destructive
operation, and at the original schedule of periodical maintenance and/or
general reconstruction of the production system, one can dismantle the
sealed facility, change the leaky seal in it or adjacent to it and reuse the
facility without the sealing fitting.
Back to top ...
An Information sheet - sprayed metallizing
The field of sprayed metallizing is a very wide field, and in this sheet, we
will concentrate on the main things and their essence. First we should
separate between hot sprayed metallizing and cold sprayed metallizing.
Secondly, we should separate between coatings for maintenance and
renewal of equipment and coating as a preventive treatment.
1) Hot coatings are usually in high levels to resist high abrasion. In this
method, the coating material is sprayed on the equipment to be coated and
then the sprayed material is melted on the equipment. It is
customary to use this method to coat parts of grinders, worms to handle
abrasive materials, sliding seats for mechanical seals, sleeves of pumps,
repair of broken or faulty casting parts and so on.
2) Cold sprayed coatings - this is a coating method which great
advantages are two:
One, we can use it to renew equipment without heating it to a temperature
that will distort the equipment. The second advantage is that we can
coat almost any material with any material we choose. For instance:
a bronze coating of a segment of a steel shaft in order to smoothen it, or
an aluminum coating of a steel surface for protection against various
kinds of chemicals. The connection between the coated equipment and
the sprayed material is a mechanical connection based on the
preparation of the surface in a certain geometry which geometrically
locks the sprayed material and the coated body. There are plants which
are still afraid of this technology. The answer to those is
professionalism! If coating is performed properly with no "cut-off's",
then success is guaranteed,

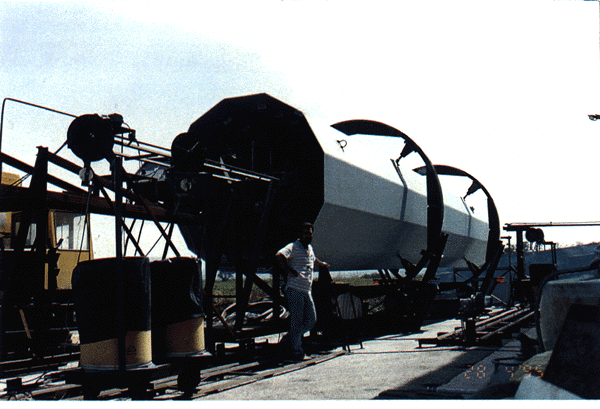
3)Coating for maintenance and repair of equipment
damaged during work.
Occasionally, at the time of dismantling a shaft from a machine it turns
out that the bearings' seats are damaged or that the sliding surfaces of the
seals are scratched. Instead of producing a new part which is a lengthy
and costly possibility, there's the alternative
implemented by Metal-On which is a coating that is more durable than the
original part itself! Many are choosing to use the alternative of welding
without taking into consideration the accompanied results. This usually
happens in places where a service party handling a certain field also,
perform the mechanics jobs. For example, a skilled engine winder who
handles a faulty shaft solves the problem by a filling welding and a
change of a bearing. The problem is apparently solved, yet this is not
true, since the welding of the shaft results in several problems:
A. Stresses are introduced into the shaft, and might be inadvertently released.
B. Minor distortions are introduced to the shaft and take it out of balance.
C. In the welding area, welded in a random electrode, a weak failure area is created.
In conclusion, an unprofessional repair of a well-winded engine will result is
a low reliability and short life.
4) Coatings as a preventive treatment -
the cold coatings as well as the hot coatings
are suitable for usage as a preventive treatment. In the chemical industry there are
numerous tools made of steel and coated with aluminum, stainless steel and other
materials as a protection against chemicals which exist in these tools, such as:
tanks, reactors, air passages etc.
In the industry, coatings are performed as a mean of protection against nature
damages, for example: the new utility poles of the Israel Electricity Company
are cylindrical poles of a diameter of about 3500 mm internally and externally
coated in an automatic coating with a sprayed melted zinc coating;
underground pipes (in large diameters) are coated with a sprayed melted zinc
instead of galvanizing. Large storage tanks, stationed nearby the sea are also coated with zinc.
Back to top ...
Protection against erosion Blower's
blades and surfaces of blowers' bodies are coated with erosion resistant
materials, and there are numerous other examples. Recently, knowledge
has been acquired in the field of industrial boilers. In most cases, the piping is
damaged by the combustion inside the boilers or ovens. A leakage in one of the
pipes might result in the stoppage of an entire plant. These phenomena has
occurred and the results are known.
Through the knowledge and new equipment purchased by Metal-On, it is
possible to perform a protective coating of the piping inside the boiler and thus
prolong the piping life, without affecting the heat transfer. This technology is
being implemented in the last years in most of the European countries.
Back to top ...
Manufacture of handling systems
In this field, Metal-On is performing projects of design and manufacture
of handling systems alike conveyors for plane handling, worms to handle
powdery materials, grains, belt conveyors, link conveyors and elevators.
Some of these projects are performed for the food industry and therefore
they are made of stainless steels and polished in a polish degree suitable
for the food and dairy industry.
Sometimes we perform worms where the blade edges of the screws are
coated with a hard coating to resist abrasion. These projects are
performed for various degrees of loads as well as for varying degrees of
loads and transfer.
Dynamic balance
Back to top ...
Dynamic balance
In the infrastructure of performing maintenance and coating works of
rotating equipment, the need arose to examine the degree of balance of
the treated equipment.
Therefore another line of Metal-On is the field of dynamic balance.
The company workers were trained abroad to work also in this field, by using
electrical computerized equipment to balance shafts, blowers, pumps,
accelerating belt wheels etc., without dismantling the equipment. One of
the company's engineers is in charge of this field and he is the one
performing this service.
Back to top ...
Repair, reconstruction and establishment of machinery
Metal-On employs outstanding professionals in the field of mechanics,
therefore it has a respectable place in the field of machinery
reconstruction.
This field, as we know, requires a wide variety of a technical know-how,
starting from the simple metalwork, through mechanics, hydraulics,
pneumatics, machine tooling, welding etc.
In the infrastructure of reconstruction and maintenance of machinery,
Metal-On has accumulated a lot of experience in the rubber industry,
porcelain industry and food industry. Metal-On is well experienced in
reconstruction of rollers, machinery, industrial washing machines, mixers
for the soap industry and so on. Metal-On is performing and has
performed in the past a transfer of complete industrial plants from one
location to another, through dismantling them and relocating in the new
location, leveling and operating up to a working/production state.
Back to top ...
Machine tooling
In order to perform coating and production jobs in the Metal-On
Industries' workshop, we have a wide variety of equipment for machine
tooling. After
coating we perform machine tooling through turning or grinding, as
necessary.
· Turning: in the workshop we have various lathes and we can turn parts
  up to a length of 5000 mm, and a diameter of 1000 mm.
· A miller: we perform also milling jobs according to the requirements of
  the product.
· There's a slotter to cut inner grooves for splines.
· We also perform round grinding by using cylinder grinder.
Metal-On Industries is experienced in "crazy" turnings by building special
facilities for turning/milling in the field, meaning establishing a unique
facility for the purpose of performing a special machining that can not be
performed in a conventional machine.
The Metal-On company was authorized to the ISO 9002 standards and is
working according to the Quality Assurance standard.
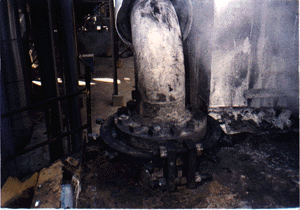
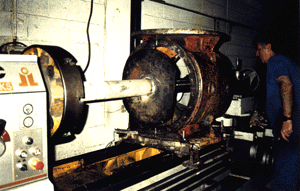
Back to top ...
"Metal-On" the site is powred by stdio
|